At Apex Ordnance, We Take Great Pride in Our Ammunition Manufacturing
Designed to ensure quality, reliability, and performance. Understanding the machinery and materials involved in creating our 5.56 NATO ammunition is essential for appreciating the craftsmanship that goes into each round. Here’s a detailed look at the machines we use and the materials involved in our ammunition production.
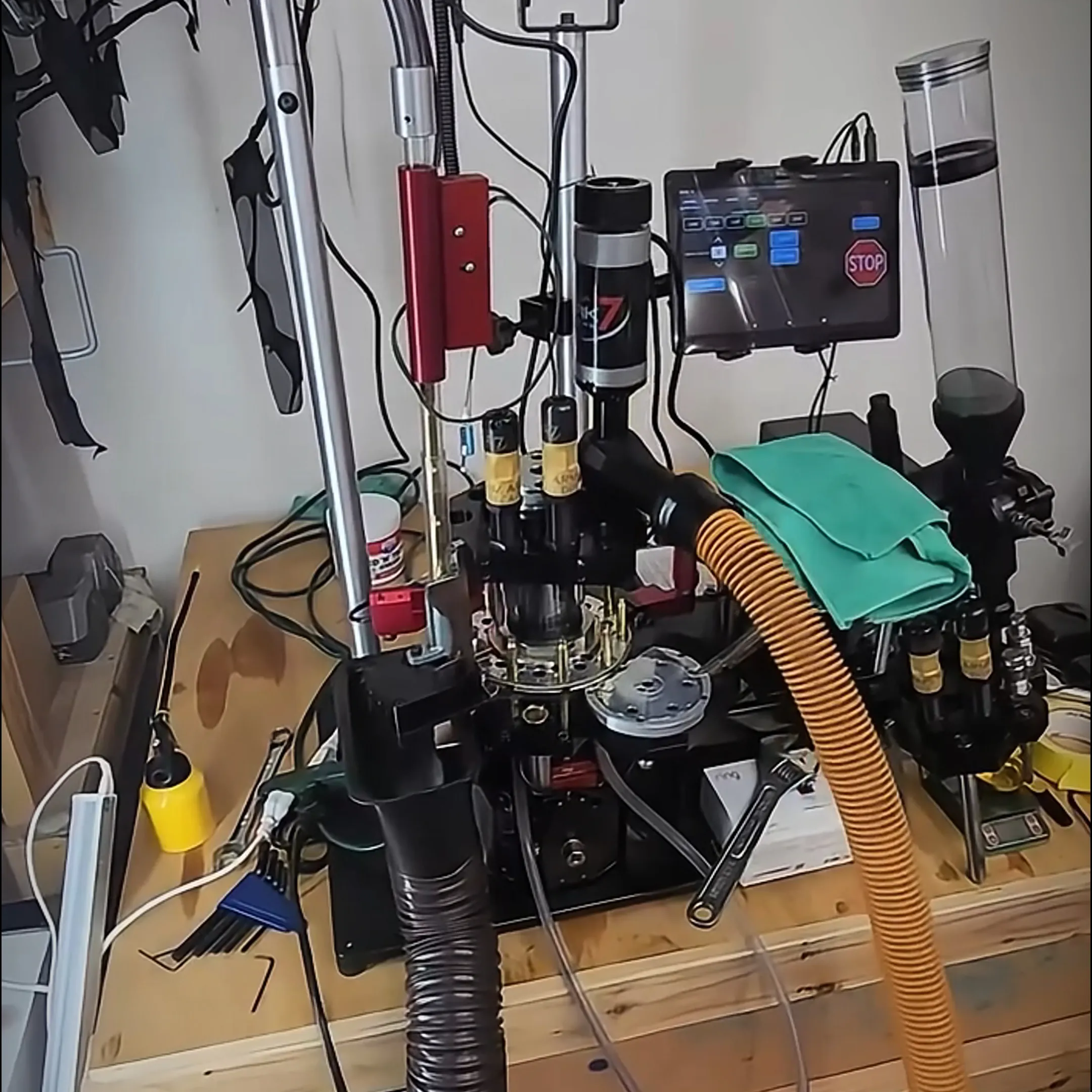
Check Out Our Best Selling 5.56 NATO Ammunition
- 19 % OFF
.223/5.56 - 62 Grain - 100 Rounds
Apex Ordnance 62 grain ammunition for .223/5.56 rifles. High-quality rounds perfect for training and target practice.
$57.95 $71.98In Stock
- 41 % OFF
.223/5.56 - 62 Grain - 20 Rounds
62 grain 3040fps ammunition, ideal for precision shooting and training purposes.
$13.98 $23.55In Stock
- 15 % OFF
.223/5.56 - 55 Grain - 100 Rounds
55 grain 3050fps rounds, perfect for high-volume training and range practice.
$54.95 $65.00In Stock
- 15 % OFF
.223/5.56 - 55 Grain - 50 Rounds
55 grain 3050fps ammunition in a convenient 50-round package.
$27.95 $32.95In Stock
The Machinery Behind Ammunition Production
The process of manufacturing ammunition involves several precise steps, each facilitated by specialized machinery. Below is a breakdown of the key stages in our manufacturing process:
1. Priming the Case
The first step involves priming the cartridge case. This is done using a primer insertion machine that inserts a primer into the case’s primer pocket. The primer is a critical component that ignites the propellant when struck by the firing pin.
2. Sizing the Case
Once primed, the case undergoes resizing using a sizing die. This machine ensures that each case meets specific dimensions and tolerances, allowing for proper chambering in firearms. After resizing, cases are checked for specifications to ensure they are within acceptable limits.
3. Flare the Case
Next, we use a flaring tool to slightly open the mouth of the case. This flaring makes it easier to insert the projectile without damaging its base or affecting its performance.
4. Powder Drop
The next step is powder dropping, where a precise amount of gunpowder is dispensed into each case using an automated powder measure. This machine ensures that every round receives an exact amount of powder, which is crucial for maintaining consistent ballistic performance.
5. Powder Check
After powder dropping, we perform a powder check using a dedicated sensor system to verify that the correct amount of powder has been dispensed into each case. This step prevents any potential issues related to under- or over-charging.
6. Bullet Drop
Following the powder check, a bullet dropper places a projectile onto each charged case. The projectiles used are typically made from lead or lead-core with copper jackets, selected for their weight and aerodynamic properties.
7. Seating
The bullet is then seated to achieve the desired cartridge overall length (COL) using a seating die. Proper seating depth is crucial for accuracy and reliable feeding in semi-automatic firearms.
8. Crimping
Depending on the type of ammunition being produced, some rounds may require crimping to secure the bullet in place within the case. A crimping die applies pressure to ensure that bullets remain seated during handling and firing.
9. Polishing
After assembly, cases are polished using a vibratory tumbler filled with polishing media (like corn cob or walnut shells) to remove any contaminants and enhance appearance.
10. Final Inspection with Go/No-Go Gauge
Each round runs through a go/no-go gauge, which is a final inspection step to ensure that all rounds meet sizing specifications before packaging.
11. Packaging
Once inspected, rounds are packaged into boxes for distribution. Automated packaging machines streamline this process, ensuring efficiency and consistency.
12. Labeling
Finally, each box of ammunition is labeled with essential information such as caliber, bullet type, weight, and safety warnings before being shipped out to retailers or customers.
Materials Used in Ammunition Production
The quality of ammunition depends significantly on the materials used in its production. Here’s an overview of the primary materials involved:
Brass Cases
Brass is the most common material used for cartridge cases due to its excellent strength and corrosion resistance. The brass used in our cases undergoes extensive processing to ensure it can withstand high pressures generated during firing.
Primers: Components and Manufacturing
Primers consist of several components:
- Primer Cup: Typically made from brass or steel.
- Anvil: A small metal piece inside the cup that provides support for ignition.
- Priming Compound: A sensitive explosive mixture that ignites when struck.
Propellant (Gunpowder)
The propellant used in our ammunition is primarily smokeless powder made from nitrocellulose and other additives that enhance performance and stability during storage.
Bullets: Materials for Performance
Bullets are often made from:
- Lead Cores: Chosen for their density and ability to expand upon impact.
- Copper Jackets: Provide structural integrity and reduce barrel wear during firing.
- Specialty Materials: For specific applications like armor-piercing rounds, harder materials like steel or tungsten may be incorporated into bullet cores.
Conclusion: Apex Ordnance’s Commitment to Quality
Understanding our ammunition manufacturing process reveals how Apex Ordnance prioritizes quality at every stage—from priming cases to final packaging. Each machine plays a vital role in ensuring that our 5.56 NATO ammunition meets rigorous standards for performance and reliability.
By utilizing high-quality materials and advanced machinery, we produce ammunition that shooters can trust—whether they’re at the range or in critical situations. For your next shooting experience, consider choosing Apex Ordnance ammunition and feel confident knowing it was crafted with precision and care.